CrankyGypsy
Jetboaters Captain
- Messages
- 352
- Reaction score
- 297
- Points
- 202
- Location
- Tampa, FL 33615
- Boat Make
- SeaDoo
- Year
- 2008
- Boat Model
- Challenger
- Boat Length
- 18
(referencing 2008 Sea Doo Challenger 180)
(Porpoising C180 - Trim tabs or pump wedge?)
(Speedster 200 Trim options - porposing)
If you own a 2005-2008 Challenger 180, you know that they come out of the water easily over waves. "Porpoising" forces you to slow down and is a huge nuisance when you want to get somewhere fast. Sea Doo addressed this issue for 2009 and those owners report less issues due to flatter and wider chines. To help the earlier 180s, they offered a pair of small trim tabs for $475 and sometimes covered them under warranty. These OEM accessories are no longer available (selling out in 2009!) and the layout of the stern prevents common trim tabs from being installed without detriment to reverse functionality.
Right now, I am just posting up a basic overview of the plate as I haven't had a chance to test it out on The Gulf against swells. Regardless if this works or not, I want it documented for anyone else considering solutions to this problem. If further tests prove positive, I will elaborate on the design and fabrication in the following post. My initial testing on Lake Tarpon seems to show an expected 1-2mph reduction in top speed. One benefit I may be noticing on the lake is the boat remaining on plane a little longer as I reduce speed.
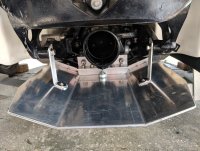
(Porpoising C180 - Trim tabs or pump wedge?)
(Speedster 200 Trim options - porposing)
If you own a 2005-2008 Challenger 180, you know that they come out of the water easily over waves. "Porpoising" forces you to slow down and is a huge nuisance when you want to get somewhere fast. Sea Doo addressed this issue for 2009 and those owners report less issues due to flatter and wider chines. To help the earlier 180s, they offered a pair of small trim tabs for $475 and sometimes covered them under warranty. These OEM accessories are no longer available (selling out in 2009!) and the layout of the stern prevents common trim tabs from being installed without detriment to reverse functionality.
Right now, I am just posting up a basic overview of the plate as I haven't had a chance to test it out on The Gulf against swells. Regardless if this works or not, I want it documented for anyone else considering solutions to this problem. If further tests prove positive, I will elaborate on the design and fabrication in the following post. My initial testing on Lake Tarpon seems to show an expected 1-2mph reduction in top speed. One benefit I may be noticing on the lake is the boat remaining on plane a little longer as I reduce speed.
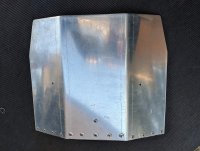
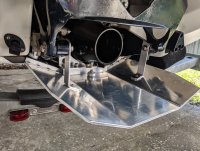
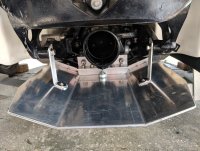