KXCam22
Jetboaters Admiral
- Messages
- 1,084
- Reaction score
- 908
- Points
- 272
- Location
- Kamloops BC
- Boat Make
- Yamaha
- Year
- 2008
- Boat Model
- AR
- Boat Length
- 23
By request I am reposting the details of my ballast build for the 2008 AR230. I have been using the system for 3 summers now with great success. There were a few minor issues and a couple of my ideas didn't workout but with a few tweaks the system works excellently. Fill time is approx 5 minutes.
My build was typical to many in terms of bags, location and such but I added some additional equipment that many won't' I will warn you now that I am an electrical engineer, so I have a tendency to make things as fancy and cool as possible. Here goes:
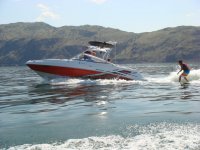
I started with a game plan:
- 2 pumps
- 3 bags
- electric valves to control the flow of water.
- fully automated to turn off when empty and full
- computer control with touch screen
- audible warning when it turns off
- fast fill times.
- as few holes in the hull as possible.
I got all my main parts at Wakemakers.
Bags:
I used the typical twin 400lbs bags in the side compartments and an 800lb in the ski locker. I have since added an 800 sumo sac aux. bag that sits on the swim deck or on the floor. We fill that one with an aux. hose and quick connector from the pump system. Preparing the inside of the rear compartments was nasty. There are a number of sharp screws in there that are not removable. I am not a small person and there is a shortage of midgets or slave children in the area so I had to crawl in there myself with a grinder and grind all the screw points off. I then installed the bags and used some vinyl decking material as a cocoon to padd the bags. Works great. All of my bags have a fly-high quick connect. It has proven to be very handy and worth installing. For the port side you have to relocate the battery and the filler hose. The battery is simple as you just move it forward 12" and re-attach, then extend the battery cables. For the filler hose I installed an eye-bolt up very high in the side wooden bulkhead and then used large ty wraps to pull the filler hose up and out of the way.
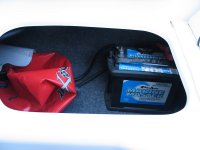
More to come. Cam.
My build was typical to many in terms of bags, location and such but I added some additional equipment that many won't' I will warn you now that I am an electrical engineer, so I have a tendency to make things as fancy and cool as possible. Here goes:
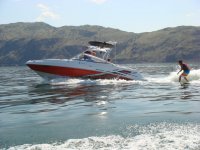
I started with a game plan:
- 2 pumps
- 3 bags
- electric valves to control the flow of water.
- fully automated to turn off when empty and full
- computer control with touch screen
- audible warning when it turns off
- fast fill times.
- as few holes in the hull as possible.
I got all my main parts at Wakemakers.
Bags:
I used the typical twin 400lbs bags in the side compartments and an 800lb in the ski locker. I have since added an 800 sumo sac aux. bag that sits on the swim deck or on the floor. We fill that one with an aux. hose and quick connector from the pump system. Preparing the inside of the rear compartments was nasty. There are a number of sharp screws in there that are not removable. I am not a small person and there is a shortage of midgets or slave children in the area so I had to crawl in there myself with a grinder and grind all the screw points off. I then installed the bags and used some vinyl decking material as a cocoon to padd the bags. Works great. All of my bags have a fly-high quick connect. It has proven to be very handy and worth installing. For the port side you have to relocate the battery and the filler hose. The battery is simple as you just move it forward 12" and re-attach, then extend the battery cables. For the filler hose I installed an eye-bolt up very high in the side wooden bulkhead and then used large ty wraps to pull the filler hose up and out of the way.
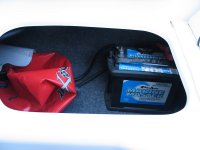
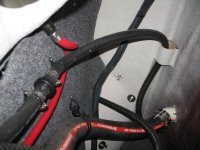
More to come. Cam.
Last edited: