svana
Jetboaters Lieutenant
- Messages
- 426
- Reaction score
- 388
- Points
- 157
- Location
- Riverview, FL
- Boat Make
- Yamaha
- Year
- 2008
- Boat Model
- SX
- Boat Length
- 23
I've always felt that the switch panel to the right of my SX230 is grossly underused and poorly designed so you can't get more than maybe one or two additional switches in. With a freshwater shower being on the "to-do" list, this was a prerequisite in order to have an appropriate place to put the switch. The new plate holds 4 additional switches and I'll use this time to replace the cigarette lighter with this much more useful socket. I printed it with PETG, the plan is to spray it with some high fill primer to lose the layer lines and cover with a metallic black as I think that's the closest match to the original plate. I'll finish it up with a couple coats of UV resistant clear coat to further protect it from the sun and elements. I'm actually surprised as to how well it printed as my printers been giving me fits. The additional 4 switches will likely cover most if not all of my future needs (I'm looking at you, fridge and inflator lol) and worst case I'll reprint a panel for my radio which is slated to be replaced anyways. I had a few leftover Contura V switches from my 4Runner which I tested them with as I'll be replacing all of my old SX230 switches with the same style as well.

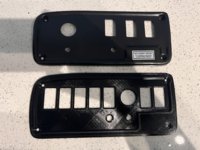
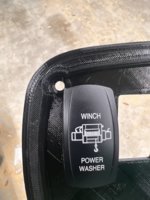
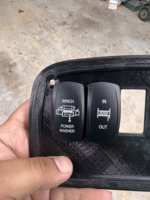

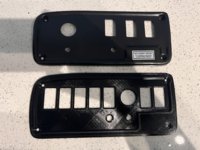
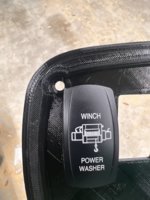
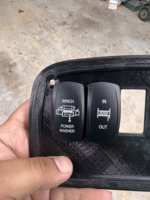