Alright, the moment you all (or maybe just a few) have been waiting for… Got the job done, actually way easier than expected. Started at 10am and probably had it done and reinstalled by 1pm. Since it didn’t take as long as I thought my buddy and I decided to install the transducer to the Hummingbird Helix 5 that I have as well. Both my friend and I are pretty mechanically inclined and I was confident with the help of the forum that we could get this done. So let the games begin..
The first step I didn’t take pictures of and that was pulling the pump, there are plenty of posts, videos, etc on doing that so no need to show everyone how to do that. This was the first time pulling a pump that I have done and it went really quickly and easily. The impeller looked perfect and the wear ring looked great as well, so that was nice. The one thing I did notice is the steering bushings were not there when I took the bolt out, we will get to that though.
The second step I did was remove the exhaust fittings, two of them pictured below, I believe they were 9/32 socket to loosen the bands. I got both those loose and was able to wiggle the middle exhaust pipe out which then gave me enough room to slide the engine forward as you see in the picture below.
The next step was removing all four TOP bolts on the motor mounts. That’s right only FOUR single bolts, I believe they were 12mm sockets. As you see below I got a couple pics of them. to get to the back right bolt you definitely have to remove that exhaust piece or else it’s almost impossible to get a wrench to (found this out when I put the exhaust piece back on before I tightened that motor mount bolt). I actually left the bolts halfway in until the next few steps were done.
Next step was removing the plastic housing above the drive shaft coupler thingy which is attached to the intermediate assembly. 10mm socket I believe. After you have that bolt out you have to pull the plastic guard towards the back, you may have to pull up on the rubber bolt thingys towards the engine, sorry no pic here but it’s pretty explanatory when you actually see them.
After I removed this plastic housing/guard is when I jiggled the drive shaft and realized how bad the bearing was, yikes haha. Next I removed the three bolts around the Intermediate Bearing Assembly. 12mm socket I believe. I got a pic of two of the bolts but not the third which is approximately where the arrow is, also remove the grease tube from the fitting here too. Just look at how much rust that water has caused….Probably has been bad for awhile so thankfully it didn’t completely fall apart while we were on the water. Something I do believe is crucial here is take a sharpie and mark where the driveshaft meets the housing assembly. The driveshaft was so loose I could move it away from the housing so I put the couplers together and marked before moving the engine forward.
Next, we removed the engine mount bolts completely. We weren’t sure how heavy the engine would be or more so how hard it would be to slide forward. Decided to use some heavy duty dock lines to go through the three rings on the engine as pictured below. This was way easier than we thought, I was sitting on the seat above the battery and my friend was kneeled down on the fuel hatch, we pulled slowly and it slid forward. We also put two 4x4 pieces of wood down below, not sure they would’ve helped after putting them there but oh well.
Next was pulling the intermediate assembly off, it was stuck on there pretty good so using a hammer to tap on it a number of times finally got it to come loose. After it came off we had to slide the engine ever so slightly forward more, as you can see in the pics above we moved the engine around 1.5-2in. Obviously you need to be cautious in that step so take it slow and check constantly. I didn’t have any pics of me removing the assembly, didn’t think we needed to.
Thank god a mechanic we knew who was just a few blocks away had a 20 ton press (harbor freight) since my buddy couldn‘t get into the county shop and use that. The old housing and bearing was shot I’ll post a pic of it below, not sure if Beachbummer will still want it? Anyhow, measured the one side of the driveshaft coming out of the housing with the micrometer (both pics below, measure top of driveshaft to where it meets the housing), pressed the shaft out of the old, added grease to the new housing & drive shaft to help when it was pressed, and then pressed it back into the new assembly. I did clean up some of that rust on the drive shaft and the housing area where the bearing housing goes into.
So I didn’t really get any pics of reassembly because it’s obviously in backwards order. I hooked the tubing to the housing before I bolted it back on to grease the bearing, I know scary because greasing=bad lol. After I got some grease to come out of the tubing again, I hooked it up and gave it 5 pumps and called it good. I bolted the intermediate assembly back to where it goes. There’s a couple pins for lining up purposes, I had one still on the housing that the assembly goes on and then the new assembly came with more pins to replace the old ones. Sorry no pics here but it‘s easy to see once you’re doing it, it’s literally fool proof. I did add a tiny bit of gasket sealant on the back of the assembly before bolting on, probably don’t need it but felt it was needed. Place the grease tubing back on the housing fitting.
The next step was pushing the engine back to the assembly and engine coupler. I lined up the teeth (if you wanna call them that) to match with the engine when we moved it back. This made us think for a bit because some of the shims were misaligned. I could push the engine back myself, so what we did was I pushed it back a little bit and we then tapped the metal shims with a hammer and they slid right where they were supposed to go. We repeated this a couple times and got the engine aligned perfectly, shims perfectly, and then the motor mount bolts were placed and tightened. Below is a picture if you zoom in on it you can see the shims are slightly misaligned. Once you move it back the top shim seems to stay where it is, so just tap it in, just give it a little tappy tap.
I then wiggled that exhaust piece back into the rubber fittings, it can only go one way, if you look above there’s like a small key on the top edge of that exhaust pipe, it slides into that rubber fitting nearest the engine like that. After that was in I tightened the clamps. We then had some celebratory beers, the hardest part was done, putting the pump back in would be a breeze. I don’t like the Busch apple, For the record. Thank god I bought the bushings from Bruce many months ago for the steering linkage, since my bushings were missing, not to mention the damn bolt was flipped so we had to actually remove the bolt holding the CobraJet Steering on. We flipped this bolt around after the bushings were added, you’ll see in the picture below just a tiny bit of the blue material Bruce uses to print them. I am excited to see how much of a difference it will make in steering!
Since we had some spare time here’s a pic of the transducer we installed. Used an existing hole, sealed the old ones, and drilled two new holes for the mount. Had to take the clean out tray off obviously to run the transducer wire. Cut the old wire, taped the new wire to it and pulled it to the helm. Used a bunch of heavy duty silicone to seal the through hole under the clean out tray since the parts store didn’t have 3M 4200. If it doesn’t work I’ll redo it but it should hold fine.
All in all, I think about anyone could do this job. I am 5’8” and 160lbs, so I can fit in tight spaces pretty well, I didn’t really think it was all too hard to get to any bolts. I will gladly help anyone in any way with doing this job. I plan to replace the other bearing in next year’s offseason just to have peace of mind. It felt sturdy without play when I messed with it but still skeptical how long it will last even though it isn’t leaking at all. I did use some medium loctite on the motor mount bolts and intermediate housing assembly bolts. Didn’t feel it was necessary for the pump bolts because I plan to grease the cones in the offseason, didn’t have any Epnoc grease on me to do it today. Just glad this job is done and was much easier than expected. Thank you all and all previous forum posts for guiding me. Thank you to CJS Jeff for answering my messages quickly when I had a couple questions prior to doing the job. I hope this step by step guide with photos gives the next person confidence in doing so! Happy boating everyone!
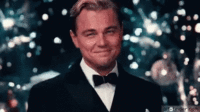