Ok, so my next phase in this project is trying to figure out how I can utilize the No Wake Mode functionality. Do I really need it? Not really, but it would be nice to somewhat bring my 20th century boat a little bit more into the 21st century.
My understanding of the boat's no wake mode is that there are two wires in the boat's no-wake switch. When the no-wake switch is "off" the wires are connected together, with essentially no resistance in the circuit. When the no-wake switch is on, the current then passes through a 4.7k Ohm resistor. The ECU sees this resistance in the circuit, and knows that means to activate the no-wake function. The circuit either has no resistance, or some resistance, but the circuit is never open (infinite resistance). The circuit is always closed, and varying the resistance in the circuit tells the ECU whether or not it needs to be in Low Wake mode or not. An open circuit indicates a problem to the ECU.
I suspect that the no-wake mode in the skis probably operates in the same fashion. There is a blue wire coming from the remote security box that goes directly to the ECU. In bypassing the security box, that blue wire must be grounded, otherwise I could not get the engine to start. So once again, no resistance tells the ECU that things are ok, and infinite resistance (open circuit) tells the ECU that there's a problem. I suspect that if I introduced the correct amount of resistance between the blue wire and ground, I bet I could get the No Wake function to activate. The problem is, I don't know what resistance the ECU is looking for.
In an attempt try and figure out what the resistance might be, I dissected my security box since I no longer need it. I am not an electrical guru by any stretch of the imagination, but I decided to take this thing apart to try and see if I could find any clues. The security box was filled full of this rubberized material with small rocks in it. I dug out as much as I could with a screw driver, in hopes that I would find a resister. Unfortunately, I did not find a resistor, but I did find a varistor, which as I understand it, varies its resistance as voltage changes. Ok, that doesn't really tell me much, so it looks like I'm going to try trial and error to figure out what resistance the ECU needs in order for Low Wake Mode to activate. I have a 10k Ohm potentiometer, which basically allows me to vary the resistance using a dial. The idea is that I will start the motor with no resistance on the pot, then as motor is running, slowly increase the resistance while monitoring YDS to see if I can get Low Wake Mode to activate.
Fingers crossed...
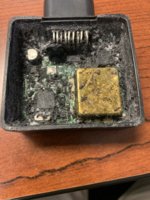