3D_Print_'em
Member
- Messages
- 2
- Reaction score
- 2
- Points
- 12
- Boat Make
- Other
- Year
- 2024
- Boat Model
- Other
- Boat Length
- Other
Hi all,
I have been looking for feedback on multiple forums and came across this one and need some more feedback or suggestions for my 3D printed jet boat.
I am making and designing a scaled down electric jet boat for a school project and am focusing on the engineering and development of the propulsions systems. This involves the intake which directs water towards the impeller and is then driven to the end of the jet where the velocity of the water builds. I just need to know if the design I have made would work for this scale boat and what concepts I have to keep in mind while designing the rest of the Jet pump.
Here is a photo of the intake:
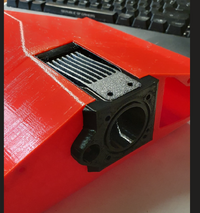
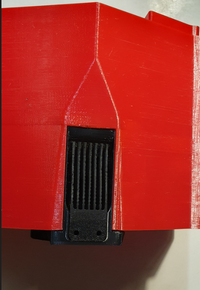
The impeller I have designed is driven directly by a brushless motor and is coupled to a shaft which spins the 3D printed impeller. After seeing how others design an impeller, I made the diameter of the shaft increase towards the end of the jet pump to allow the blade pitch to increase and drive the water out faster. Here is my design of the impeller: It is a two-stage impeller in order to reduce the cavitation of the water around the impeller.
Any feedback or suggestions are greatly appreciated,
Thanks
I have been looking for feedback on multiple forums and came across this one and need some more feedback or suggestions for my 3D printed jet boat.
I am making and designing a scaled down electric jet boat for a school project and am focusing on the engineering and development of the propulsions systems. This involves the intake which directs water towards the impeller and is then driven to the end of the jet where the velocity of the water builds. I just need to know if the design I have made would work for this scale boat and what concepts I have to keep in mind while designing the rest of the Jet pump.
Here is a photo of the intake:
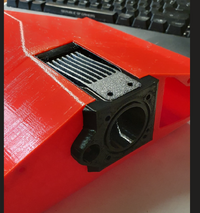
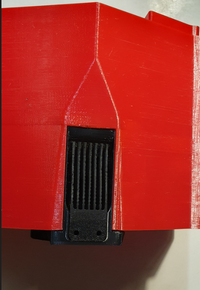
The impeller I have designed is driven directly by a brushless motor and is coupled to a shaft which spins the 3D printed impeller. After seeing how others design an impeller, I made the diameter of the shaft increase towards the end of the jet pump to allow the blade pitch to increase and drive the water out faster. Here is my design of the impeller: It is a two-stage impeller in order to reduce the cavitation of the water around the impeller.
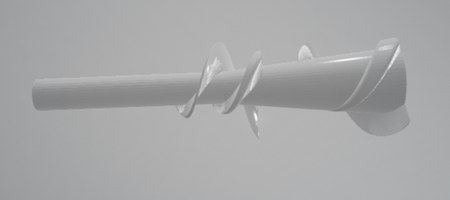
Any feedback or suggestions are greatly appreciated,
Thanks