It's been pretty crazy over the holidays, but I definitely wanted to come back and update this thread! I was able to get everything sorted finally! Thanks again for everybody's advice and suggestions here. I learned a lot in this process.
I ended up calling a local Marine shop that has been around for years (Art's Marine in North Little Rock, AR). Years back they worked on an outboard motor for me and were always super friendly and helpful. They don't work on jet pumps, but I explained my issue and they immediately gave me a number of a local mechanic that has a shop at his house and works on Wave Runners, Dirt Bikes, etc. in his free time. He was only about 20 mins away from me and was a great guy to deal with. I dropped off the pump with him and I had it back with the impeller off within 24 hrs!
He said he didn't have to heat it up or anything but it took a VERY long cheater bar and a quick motion to free it. He estimated it had something crazy like 600 lbs of torque on it! After he got it removed he inspected the drive shaft for any stress fractures or warping and all looked good. He also removed the cone and checked the grease and bearings. He was going to put the new impeller on as well, but when checking the clearance with the wear ring, he confirmed that the wear ring would have to be replaced and he didn't have the tool to remove the old one. All in all he only charged me $45 for the removal and I picked everything back up.
He agreed I could try the dry ice trick to remove the old wear ring, and freeze the new one for installation. So with every thing back at my house and the new Yamaha wear ring in the freezer overnight, I picked up 5lbs of dry ice and packed the wear ring/housing. I could hear the and see the old wear ring contract some, but even after about 1/2 hr and multiple attempts to pulled it out with a pair of vice grips, it would still not budge! Lucky me! I ended up using a battery powered Dremel tool with several cutting wheels to cut the old wear ring through and then pull it out with vice grips. (took a few charges on the Dremel battery!) I would have loved to have had a grinding wheel handy for this step.
Once the old wear ring was removed, I cleaned every thing up good on housing and put a couple small thin lines of grease to help the new ring slide in easier. Took the new wear ring out of the freezer, quickly lined up the notch and tapped the new ring into place with a rubber mallet. Once that completed I applied some white thread sealant to threads on the drive shaft, and threaded the new Solas impeller on and tightened with a wrench. The mechanic that removed the old impeller told me to just get the new impeller tightened as much as I could by hand with a wrench and not to be concerned with torqueing it to the specs in the manual as it's reversed threaded anyway and will tighten further when spinning from the engine torque.
I then cleaned off all the old gasket maker/sealant applied new gasket maker and re-installed the jet pump. I did apply new Yamaha Molybendum grease to the splines of the driveshaft before re-installing. I'll re-iterate to be very careful when tightening the bolts down, particularly the 5th small bolt on the left side of the housing......I only tightened it by hand after applying thread sealant and the small one snapped on me! I had to pick up some bolt extractor bits to safely remove it and replace with a new bolt the same size. Luckily, the extractor bit made quick work of removing the snapped bolt.
While I had everything apart and was under the boat, I noticed that factory didn't do the best job with silicone when sealing the intake grate. One side had a pretty messed bead of excess silicone, so I carefully resealed with new black silicone, making sure everything was as smooth as possible with no gaps of missing silicone. Cleaned up any excess silicone with Q-tips and acetone.
Once everything was re-assembled and I allowed a few days to ensure the gasket maker was fully cured, I hooked the boat up to the hose in the driveway and ran it for about 10 mins. It started up and ran fine, and all water that came out of the pissers was totally clear. I won't be able to test it on the water until May, but everything appears to be back in good mechanical order.
Now I will move on to cleaning up the surface scratching on my keel!

Luckily, there was no damage into the fiberglass, a few scratches are too deep to just wet sand out. A spectrum patch paste kit or two should do the trick followed by a wet sand and polish.
Below are some pictures from the different stages of the process.
Intake Grate with messy/missing silicone from factory
Resealed Intake Grate (all black silicone is smooth with the intake grate surfaces)
Old Wear Ring Cut Out with Damaged factory impeller removed
New Solas Impeller Installed
Fun with the Jet Pump Housing snapped bolt
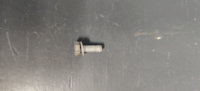